Next
Cigars: Tobacco Pipe | Cigars | Other Handmades | Davidoff Cigars from seed to ash | Next | Next | Next | Next | Next | Next
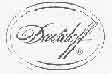 9-THE EXPERTISE OF THE MANUFACTURER
This includes the following:
The perfect condition of the tobacco leaves
The tobacco content of the cigar
The experience of the cigar roller
The quality controls
Once the leaves have sufficiently aged, the are then rehumidified so that they are more flexable. The leaves are slightly sprayed with water and then left for 24 hours covered with sacks. The next day, workers remove the stems from the leaves.
For the Ligero leaves, the stem is removed manually just by pulling it. The Liggero leaves are always used as the first leaf at the center of the cigar. They are slow burning and also will ensure a good airflow when you are drawing on your cigar and give a good construction base as well. For the binder leaves, Volado, the stem is removed mechanically.
After being rehumidified, the wrapper leaves are sorted by size and colour. They are then rolled and stored in a cool area.
Once the stems have been removed from the leaves, the leaves for the filler and the binder are sent to the blending room. In that room, the experienced blenders are putting together the correct blend and quantity of tobacco leaves to make 25 cigars of one type.
In blending, there is always a minimum of 25% of one type of tobacco.
Ligero, Seco and Volado tobacco are used for filler. Volado leaves are normally used for the binder. For the wrapper, Connecticut seed tobacco is used.
On a daily basis, the Cigar Roller is given the necessary tobacco to roll around 200 cigars. The Cigar Rollers work in teams of 2 people. Both of them are professional rollers. They roll the filler and the binder (the top of the leaf is always at the bottom of the cigar). They will then put the cigars in a mould. A mould holds ten cigars. The cigars are then pressed for 20 minutes, turned 45 degrees, pressed for a further 20 minutes, removed from the mould and the mould and outside wrapper is rolled around the cigar.
Once the cigars are rolled, they go though a quality control process. The control consists of ensuring that the cigar is well constructed and that both the diameter and the lenght are correct. For a cigar of 43 ring gauge, an acceptable cigar will have a ring gauge between 42.7 and 43.1. A cigar roller will roll up to 200 cigars a day. A 95% accuracy rate is required.
As mentioned befor, the top of the leaf is always at the foot of the cigar, meaning that the foot of the cigar contains more nicotine. This is one of the reasons that the strength of the flavours increase when we smoke the cigar.
|
 |
Cigars: Tobacco Pipe | Cigars | Other Handmades | Davidoff Cigars from seed to ash | Next | Next | Next | Next | Next | Next